Projects & Consultansy
Erection and Commissioning support
- KAMCO also can take-up Erection and Commissioning of new ESP & Bag Filters .
- ESP shutdown and repair works like changing of ESP Internals and complete repairs of mechanical and electrical items.
- Site Fabrication of structural items.
- All electrical and instrumentation works.
- Thermal insulation and cladding.
- EPC and Turnkey Projects.
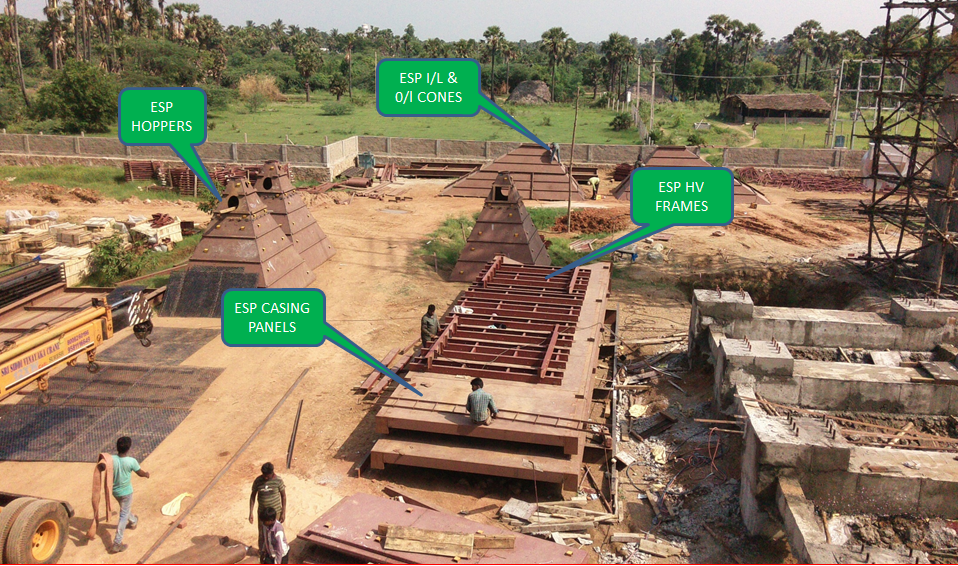
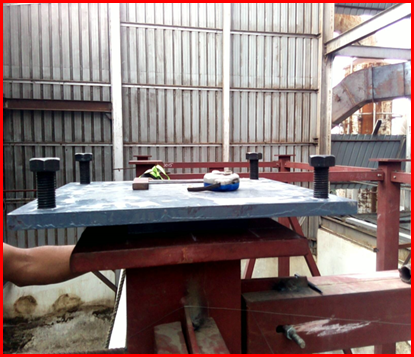
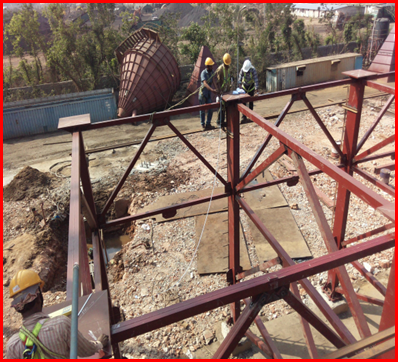
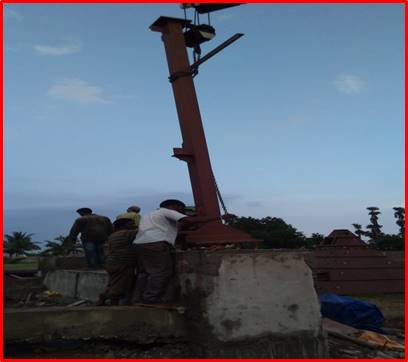
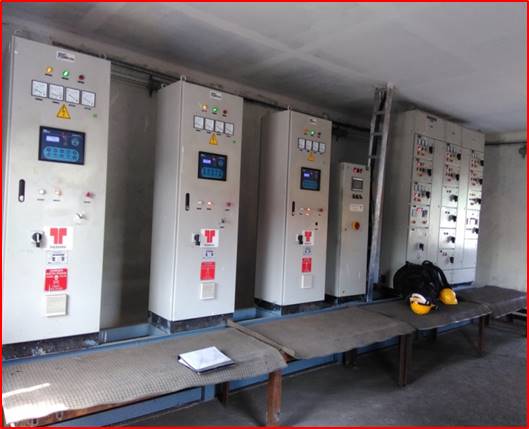
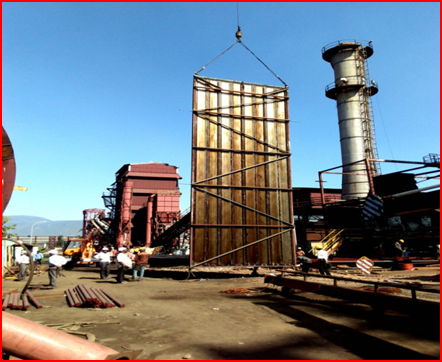
Performance audits & Digonistic Study
Inspection of ESP :-
- Inspection of the Entire equipment from inlet flange to outlet flange, which include following components.
- All structural parts including casing ,support structures, expansion joints at inlet & outlet flanges, pent house, bearings ,platforms, Hoppers est.
- Checking Alignment of Collecting Electrode and Emitting electrodes.
- Insulators (support & Shaft).
- Purge air blowers with motors.
- Rapper coils and its Assembly.
- Transformers.
- Hopper heating systems (Where ever applicable).
- RAVs & Motors.
- All electrical & Instrumentation components.
Inspection of RABH & PJBH :-
- Inspection of the Entire equipment from inlet flange to outlet flange, which include following components.
- All structural parts including casing ,support structures, expansion joints at inlet & outlet manifolds , bearings ,platforms, Hoppers etc.
- Inspecting each module for healthiness of bags and thimbles.
- If broken bag detector is not installed. Identification of modules for any bag failures to be carried out before shutdown by closing the respective modules and checking the stack emissions.
- Checking for proper bag tensioning.
- Checking for proper function of Operational interlocks.
- Poppet dampers, Dilution damper, RA dampers operation.
- Checking healthiness of Instrumentation of baghouse.
DE-DUSTING System :-
Checking Adequacy of Bag filter Capacities
- Identifying the Vent points associated with each bag filter.
- Calculating desired vent volumes at each vent point.
- Arriving at desired volume for Bag filter and checking the adequacy of existing bag filter.
- If bag filter is adequate, measuring vent volume at each point by checking duct velocity.
- Checking velocity at ID fan Inlet.
- If bag filter capacity is not adequate propose bag filter for desired capacity.
Inspection of Bag filters
- Visual inspection of the equipment. Check for any abnormalities, vibrations or sounds or any Observation of physical damages.
- Check the stack emissions and in case of visual emissions necessary trouble shooting suggestions to client
- Check the operational parameters like DP of the bag filters, Temperature, Header Pressure.
- Checking healthiness of instruments, interlocks and items as mentioned below
- DP switch/guage/Transmitter,
- Pressure switch/guage/ Transmitter,
- Temperature elements,
- Hopper heaters &Thermostats,,
- Inlet cum By-pass damper
- Solenoid valves Timer panels
- Level sensors and its controller
- Rotary Airlock Valve.